How Is Aluminium Made
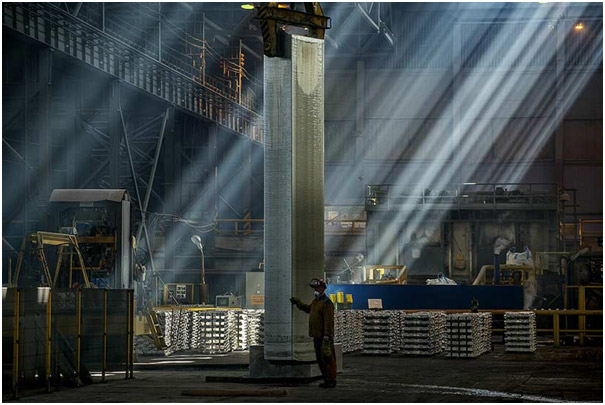
Aluminium which is also spelt as aluminum, it is a type of metal that is silver in colour that is quite soft when compared with other metals. Aluminium is one of the easiest metals to make as it is easily found within the earth’s crust. It’s a popular metal as it has a low density and has resistance properties which protect it from corrosion whether it is cause by environmental factors or cause by mechanical factors.
The Manufacturing Process
Aluminium is often found mixed in with other compounds, these compounds need to be separated which will leave behind Pure Aluminium. The compounds which are found in Aluminium cannot be simply melted away like it can with other metals like Iron, it needs to go through a much more thorough process which involves the use of a lot of electricity. Aluminium process requires the use of specifically designed smelters like hydroelectric power.
The process begins by “Bauxite Mining” which has three main stages.
- Bauxites are mined from the ground, Bauxite contains aluminium.
- The Bauxite which has been collected must be processed. The process will create alumina or aluminium oxide. If there is around 5 tonnes of bauxite collected it can process around 1 tonne of aluminium.
- Electrolytic reduction uses electric currents on the aluminium oxide which turns it into pure aluminium.
Bauxite is one of the most common minerals in the world which can be used to make aluminium. If a piece of bauxite is made with over 50% aluminium oxide it is considered to be a high in quality. Though, there are also other minerals which can also be used which contain aluminium oxide. Bauxite can appear in different colours including yellow, dark green, grey and white which can also be found mixed with other colours like purple, red, blue and black. The countries were Bauxite is located includes Australia, India, Brazil, Jamaica and Guinea. Bauxite can be mined in open pit mines and underground mines. The bauxite is removed by cutting off the top layer, it is collected and then transported for further processing.
The Bauxite which has been collected must be processed to produce alumina or aluminium oxide which both look like white powder. The most commonly used way to process Bauxite is by something which is known as the “Bayer process” which has been used for well over a hundred years. Only high quality Bauxite can be processed by using this method. The Bayer process includes the following steps:
- The crystallised aluminium hydrate is dissolved from the Bauxite in caustic soda (NaOH) at high temperatures.
- The temperature is lowered after the concentration increases.
- Before the concentration is completely cooled, the concentration may be made up of aluminium hydrate which will eventually crystallise and ballast (red mud), the ballast can be removed before the aluminium hydrate fully crystallises. Ballast can be a mix of iron, titanium, silicon and other ingredients – the Ballast is then placed in disposal which prevents the mixture from contaminating the earth. Though some companies rather than disposing the Ballast use them as raw materials for other products.
Other materials which alumina can be made from include Nepheline and Cryolite. Alumina can be stored for an unlimited amount of time if proper storage methods are used. If it is noted stored correctly it can immediately absorb water, this is why Alumina is quickly transported to a smelter as soon as it is collected.
Another method which is used to make alumina is “sintering” which takes a solid material like Bauxite and sinter it with soda and lime at a high temperatures. The soda and lime bind silica so it becomes insoluble which allows the alumina to be separated.
The next step in the production of Aluminium is to use electrolysis but in order for it to work it need a material known as Cryolite which is a mixture of hydrofluoric acid, aluminium hydroxide and soda. Once they have collected enough Cryolite, they then use Electrolytic reduction to create aluminium.
The reduction area requires a large amount of space which are multiple buildings that contain pot or reduction cells which all have power supplies that runs on 4 to 6 volts with an amperage from 300 onwards. The pot or reduction cell is filled with molten Cryolite which allows it to go up to a temperature of 950oC. Every half hour the Alumina which was collected is placed into the pot or reduction cell, electrolysis is used to separate the oxygen from the aluminium which will settle at the very bottom of the pot.
The molten aluminium is removed from the pot or cell with a vacuum which makes a hole at the top of the Cryolite which sucks the aluminium out in placed into a storage bucket. It is then taken to a Casthouse so the aluminium for smelter. This process removes the excess metals that are still found within the aluminium which may include iron, copper, silicon and others. These metals must be removed as the smallest differences can cause the end product to have varying properties. The aluminium is then placed into a furnace which has been specifically designed for this process, which is heated to 800 oC which turns it into pure aluminium. The pure aluminium is then placed into moulds to harden. The Casthouse not only makes pure aluminium but it is also used to create the type of Aluminium Alloy. Once the mix has been created it is cast to give to the required shape.
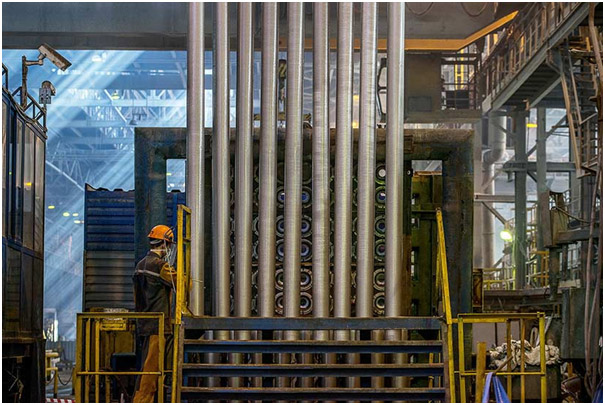
Aluminium Mixes
Pure aluminium is only ever used on its own if corrosion resistance and usability of the product is more valued than the material’s hardness. Aluminium is usually mixed with other types of metals which help improve the quality of the material which turns it into an Aluminium Alloy. When it is mixed it is known as an alloy which is graded by name in a number system like American National Standards Institute (ANSI) or is named by what it is mixed with like DIN and International Organization of Standardization (ISO) systems. Since there are so many different mixes of Aluminium its strengths, density, corrosion resistance, heat transmission and hardness vary depending on what is used.
To make the metal stronger, small amounts of scandium, zirconium, or hafnium are added to the mix. There are a lot of other elements which are used to create Aluminium alloys include titanium, chromium, copper, nickel, magnesium and manganese. This means that the person who is making the product must invest time and knowledge in understanding what mixes are best depending on what specific purposes the end product will be used for. The Aluminium’s properties are also impacted by how the product is made. For example, whether it has been heat treated or the way it has been manufactured.
During the production of Aluminium, an important aspect that must be taken into consideration is that aluminium alloys react quickly to heat. In fact, like most other metals like steel which glow red when they are subjected to intense heat, Aluminium does not glow red first instead it begins to melt, this means that the person who is manually using Aluminium needs to be particularly careful when they are using it. Since Aluminium can melt at lower levels of temperature, the design process must be strictly controlled with careful precision of temperature when it is heat treated and when it is cooled off.
Aluminium is used within products including packaging for beverages or food, in the construction of buildings including its use in roofing, doors and building wire, it is used in vehicle construction of cars, trucks and aeroplanes, it is used in the external design of electronic products like cameras and it is used in household cooking utensils. It is also used in many sex toysincluding Pipedream’s Pure Aluminium Range. You will be able to buy aluminium sex toys including chastity devices from BDSM Australia who offer worldwide shipping.